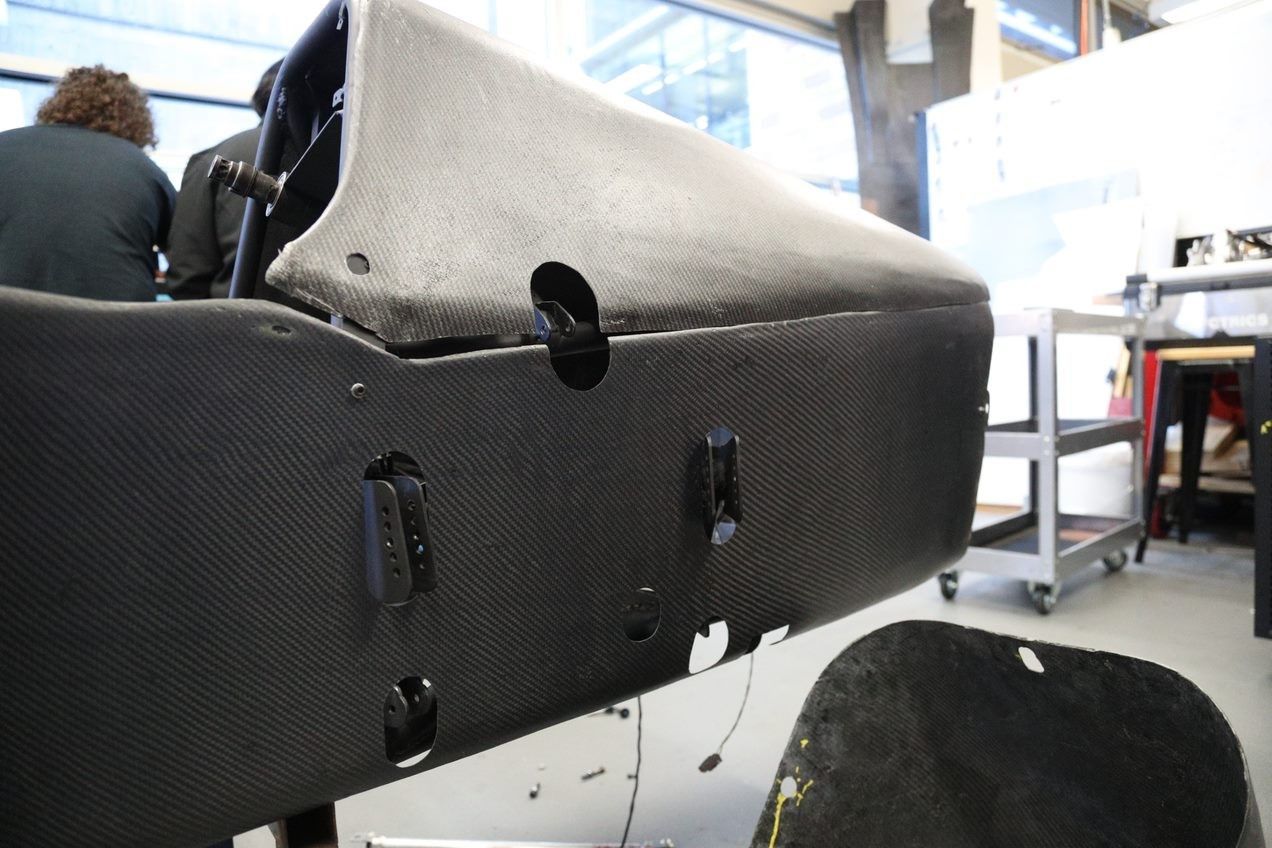
2022 Rolling Chassis and Update
Rishi Wig • September 23, 2022
Rishi Wig • September 23, 2022
A rolling chassis is a very crucial step in the progression leading to a complete car. Put simply, it is the chassis assembled with suspension and wheels (hence, rolling) sans bodywork. Redback members achieved this goal for RB21-E in Week 7 of Term 1, having completed the majority of the work from the 21st to the 27th March. In order to realise this goal, Structure's members were assigned 5 component specific tasks:
The Department collectively decided to prioritise these 5 main tasks in order to achieve a rolling chassis, due to setbacks related to the design and manufacturing process of other components. Specifically, for the control arms, members had to cut chromoly tubes to varying lengths, dependent upon their use-case. Some tubes were being manufactured for the front and rear sections of the car whilst other sets were intended to be used for upper and lower sections. The ends of the tubes were crushed using a hydraulic press, and angle ground in order for lugs to be welded onto them. Once this process was complete, and the lugs were welded on, bearings were pressed into the lugs for each set of control arms with testing necessitating the need for a complete reassembly of the control arm jig in order to double check measurements. In total, there were 8 sets of control arms requiring effort spaced out over 4 days.
To complete the steering component of the car, members were required to manufacture various parts such as the inserts, as well as cutting dampers to length in order for them to be welded together. Upon successful completion of welding, other parts such as the bearings and ferrules were fitted. The anti-roll bar involved the design and manufacturing of brackets for its associated jig as well as laser-cutting the moment arms. Chromoly tubes were again cut to specific lengths and all the components for the anti-roll bar were placed on the jig in preparation for further welding. The process of testing designs called for 4 different tube-diameter lengths, with the length passing relevant testing criteria ultimately being used as part of the rolling chassis. In total, this facet of manufacturing took around two days of work to complete.
The bell crank plates were laser cut, with spacers being lathed, and ultimately being assembled onto the car. The suspension mounts required re-manufacturing, with this process consisting of metal laser cutting the mounts and de-burring them. The manufacturing of these specific components were not as labour-intensive and as such, only took a day to complete respectively.
Upon completion of these smaller tasks, team members were able to assemble the required components onto the chassis and put the wheels on to arrive at a rolling chassis!
Electrics have a pivotal role in the creation of RB21-E. This will be a significant year, as the RB-21 will be the first official competitive operation of a fully electric vehicle by Redback Racing. As such, our Electrics department has a large number of responsibilities, which are all currently being met to the highest quality.
Battery manufacturing and setting up of the accumulator have been major tasks for the team. As the core parts of RB-21's drivetrain, these must be of high quality to ensure that power demands are met. A significant milestone has been achieved recently, with the team completing the Electrical migration of components from the RB-19 to our RB-21 car. Shifting these components for reuse is a careful process, as they must be integrated seamlessly into the structure of a new vehicle.
An ongoing process for our Electrics team is wiring. As its sole purpose is to be a method of interfacing between different parts of the system, it’s crucial for it to be well organised. Significant cable management has been undertaken to arrange the wires and ensure that they are gathered in a logical and clean manner, limiting confusion within the car’s structure.
Further work is underway to streamline the system involving the PCB. Our Electrics department has iterated through several designs to assess key targets of reliability and performance. By simplifying the overall system, Redback Racing can benefit from lesser design complexity, increased reliability (as it reduces vectors for failure) and reduced potential financial costs of excess parts.
Currently, the team is working hard and is ready to meet the deadline for the electrical readiness check at. This will be for the final checks to ensure everything is performing as expected and ready to hit the track as soon as possible.
Both Dynamics subdepartments of Aerodynamics and Vehicle Modelling are completing their own tasks alongside other departments to ensure the car is ready for the competitions at the end of this year.
The key role which our Aerodynamics sub-department is working on is the final additions of the cladding onto the car. This involves trimming (which is to help ensure that everything fits in the car’s structure) and post-processing (where the surfaces are sanded down to give evenness and remove any bumps, make sure everything is protected and prepare for the final layer). Afterwards, the final layer will be added, bringing the carbon aesthetic to the car’s surface, and helping retain the smoothness of the cladding.
CFT benchmarking is also taking place to determine the best avenues of approach for testing and development of aerodynamic structures. This takes place using various platforms, where a variety of factors are tested such as strength, convergence, and design.
Our Vehicle Modelling sub-department is assisting our Structures department with car readiness. Vehicle Modelling is working alongside Structures sub-departments, Driver Safety, on the car pedal box, and providing designs to the Linkages sub-department to help develop the control arms. More models are being created by Vehicle Modelling to further refine certain design philosophies on the car.