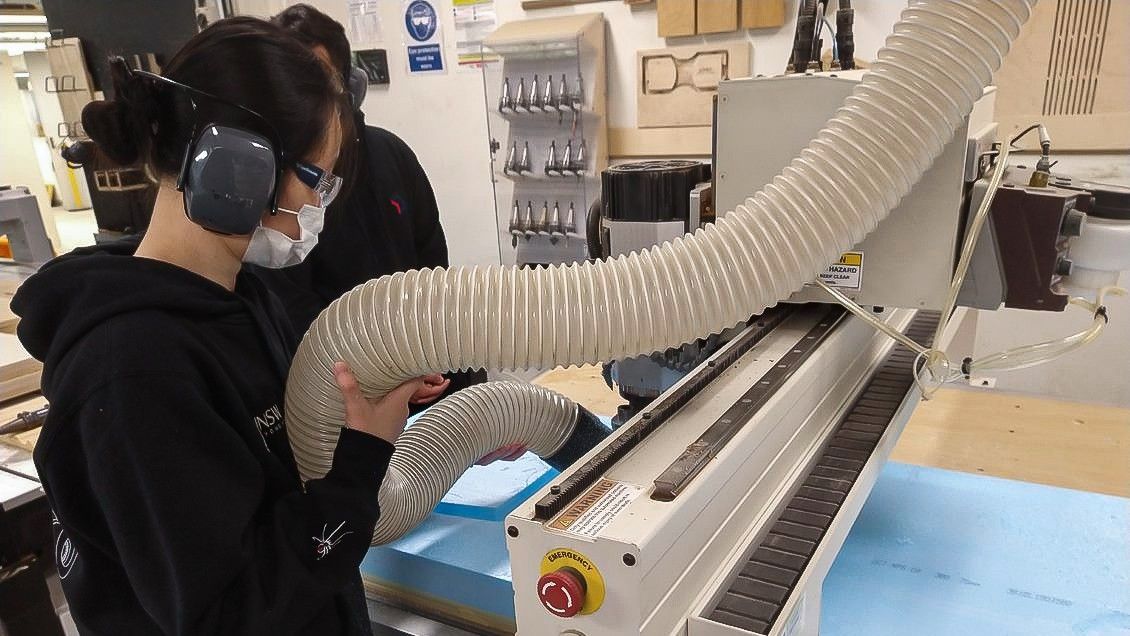
UNSW's Design Futures Lab
Rishi Wig • September 16, 2022
Rishi Wig • September 16, 2022
Redback Racing members sand down the foam cuts further to create a perfectly smooth surface. This helps in ensuring that these foam moulds will generate an uninterrupted finish once the carbon fibre is placed in.
Layers of carbon fibre are gently placed inside the foam moulds. These layups are gradually added until the required thickness of the intended cladding is created.
More carbon layup placements.
A Redback Racing member further polishes the cladding. This allows for a smoother finish and sheen, which helps assist with airflow over the car.
Further polishing.
The CNC Router follows the path programmed into it to create the intended design. The foam cuts create fine shavings, which can be utilised in further repurposing.
Different design shapes can be created by precise cutting. This can allow for intricate shapes of different depths to be created with ease.
A Redback Racing member listens keenly to the explanations and selections made by the DFL specialist. This is so individuals can gradually learn the processes and apply them when they return.
The Design Futures Lab (DFL) is a facility housed on the UNSW Kensington campus that offers a vast array of services to students and alumni. With CNC mills, 3D printers and a variety of other machinery available, the DFL is a high-quality resource with lots to give to the university community.
The DFL staff place learning at the heart of the manufacturing process. As part of this, Redback Racing members have been given an overview of how the machinery works and the ways they can operate it. Our team members will now be able to smoothly integrate their needs with their knowledge, speeding up the process and enhancing their skill levels.
DFL’s support was critical for us to meet our timeline. With accurate recreation of our designs through tool mapping, our foam blocks were able to be cut out into high-quality moulds. From there, the blocks have been taken and sanded down further to help even out the surface. These smoother surfaces will allow the carbon fibre layups to set in cleanly, giving us a uniform finish. This is critical for when the pieces are set and subsequently placed on the car’s structure, allowing for air to travel cleanly over the vehicle in testing & competitions.
To make the effort to minimise waste and maximise the utilisation of resources, waste materials are collected for the purpose of reuse. As Redback Racing made extensive use of foam blocks to create the mould shapes, a substantial amount of waste shavings has been created. Bags of these foam shavings have been collected and stored to help find a future use for the material and fashion them for reuse.
Redback Racing would like to extend a massive “thank you” to DFL for their support and assistance. Without them, we would not have been able to learn all about their services and create such high-quality moulds.